Aluminium, symbolized by Al in the periodic table, is a metallic element widely present in the Earth’s crust. It constitutes about 8% of soil and rocks, following oxygen and silicon. Aluminium is commonly found in chemical compounds with elements such as oxygen, silicon, and sulphur. The pure metal aluminium is economically produced from compounds with oxygen.
Aluminium possesses numerous properties that make it highly useful in various applications. It is lightweight yet strong, easily malleable, resistant to corrosion, non-magnetic, and a good conductor of electricity. Additionally, it maintains its strength even in extreme cold temperatures and can be easily recycled into new products.
With a production of approximately 32 million tons, aluminium is the most widely used non-ferrous metal, second only to iron in terms of quantity.
History
The history of aluminium dates back to ancient times when alumine salts were used by the Romans and Greeks for dyeing and medicinal purposes. The metal base of alum, called aluminium, was identified in 1808 and later isolated in pure form in 1827 by Friedrich Wöhler.
Pierre Berthier’s discovery that aluminium could be extracted from bauxite ore paved the way for its mass production. The Hall-Heroult process, developed independently by American and French inventors in 1886, revolutionized aluminium production and remains the primary method used today. The Bayer process, developed in 1888, played a significant role in refining aluminium ore and contributing to its mass production.
Bayer process
The process of making aluminium involves several steps. Bauxite ore, which is usually strip mined, is refined through the Bayer process to obtain aluminium oxide. This aluminium oxide is then melted in the Hall-Heroult process, resulting in pure aluminium.
The Bayer process begins with the mechanical crushing of bauxite ore, which is then mixed with caustic soda to form a slurry. The slurry is subjected to high temperature and pressure, transforming it into a sodium aluminate solution. The solution is then settled to remove impurities, known as “red mud.” The remaining liquid is filtered, washed to separate caustic soda from alumina, and transferred to tanks where alumina crystals are grown. These crystals are then calcined to remove water molecules, yielding waterless alumina for the Hall-Heroult process.
Hall-Heroult process
In the Hall-Heroult process, alumina is dissolved in cryolite at high temperature, forming a solution that conducts direct current. The current breaks the bond between aluminium and oxygen, resulting in the formation of aluminium at the bottom of the reduction pot. The molten aluminium is siphoned off and cast into ingots, which are 99.8% pure. Smelting plants typically have multiple potlines, each producing between 50,000 and 100,000 tons of aluminium per year.
Recycling
Aluminium is highly recyclable, with over 85% of the metal recovered from scrap. Recycling aluminium requires only a fraction of the energy used in primary production, making it an environmentally beneficial process. The scrap is melted and separated from slag, with the remaining slag potentially refined to extract more metal.
Applications
Aluminium finds numerous applications in various industries. In electronics, high-purity aluminium is used, while standard aluminium is utilized for heatsinks, casings, and wires. It is widely used in construction and transportation due to its lightweight and strength, serving as a substitute for steel or carbon fibre. Aluminium is employed in the production of doors, windows, siding, building wires, and as structural components in cars, trucks, railway cars, and airplanes. It is also utilized in household items such as appliances, baseball bats, cutlery, foil, and cans. Aluminium compounds have diverse applications, including absorbents, catalysts, water treatment, paper manufacturing, synthetic rubber production, and petroleum refining.
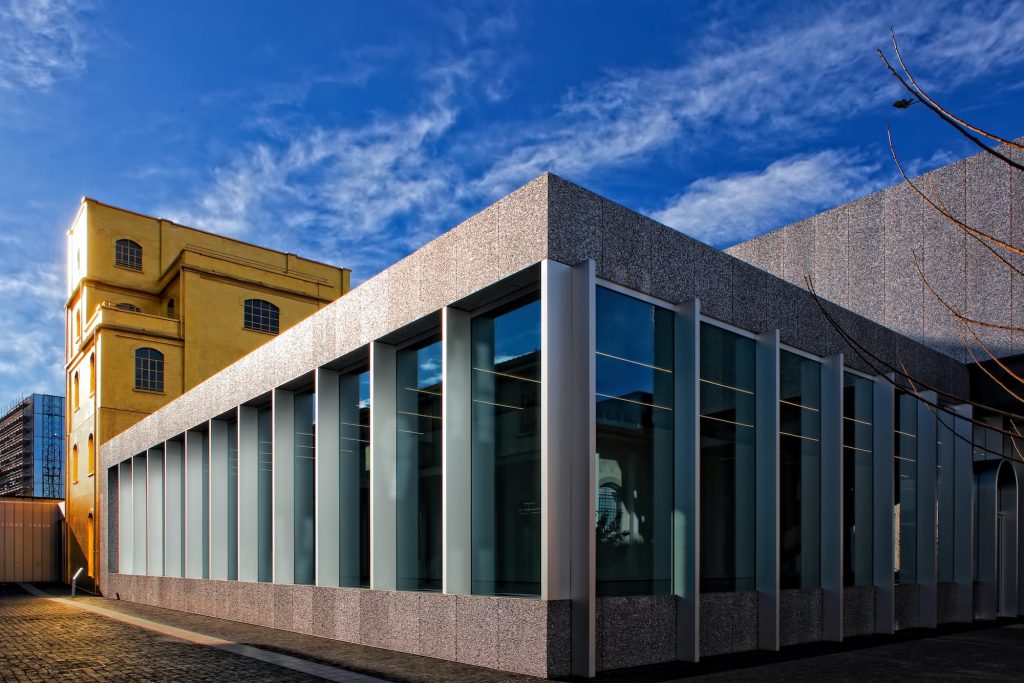
Trading
The trading of aluminium primarily occurs on the London Metal Exchange (LME), where prices serve as benchmarks for contracts. The price of energy directly impacts the final price of aluminium due to its energy-intensive production process. Additionally, the demand for aluminium, driven by its advantages in the automotive and construction industries, influences its price. Monitoring expected demand is an indicator of future aluminium prices.
LME Aliuminium Futures Contract
Aluminium futures contracts on the LME have specific specifications and terms for trading:
Product Symbol | AH |
Contract Size | 25 metric tons |
Price Quotation | U.S. Dollars and Cents per ton |
Contract Months | Monthly out to 63 months |
Tick Size | $0.25 per ton |